3D printed suppressors are extremely popular these days, but do they live up to the hype?
It’s often said that seismic levels of innovation in the firearms space are rare. Certainly, companies and individuals come up with great new ideas all the time. But sea changes that affect an entire segment of the industry don’t happen very often. The advent of using additive manufacturing—the fancy name for 3D printing—to produce suppressors is one of those key industry-wide developments.
Types Of Manufacturing
Suppressors are devices that are made of metal with specially designed geometry designed to trap, redirect, cool and slow down the gases from a gunshot, thus reducing the sound signature of a firearm, among other things.
The traditional method to manufacture devices like silencers is by machining them. Think of it like Michelangelo sculpting the statue of David—starting from a solid block of stone, he painstakingly chiseled away chips of marble to reveal the masterpiece within. CNC (computer numerical control) machines are programmed to take a block of material, such as stainless steel, and use tooling to remove material from it until you’re left with the desired component. You can then weld and screw them together into the final product. Since you’re removing material to create the desired result, this is called subtractive manufacturing.
On the other hand, additive manufacturing works in the opposite manner. Think of building up something from LEGOs, where you combine small elements to create a larger composition—like that rocket ship or race car that you made out of LEGOs when you were a kid. DMLS (direct metal laser sintering) machines use high-powered lasers to selectively fuse layers of metal powder into the desired final product. They’re controlled by sophisticated software, forming the end product out of the powder, layer by layer. Thus, you start from nothing and keep adding material until you have the final product, hence the term additive manufacturing.
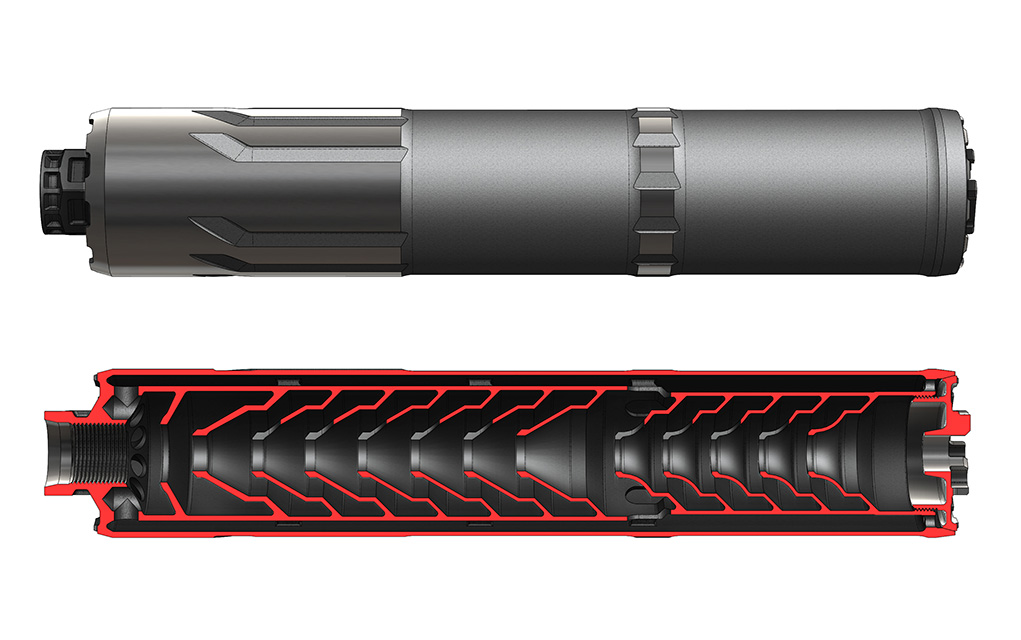
The key advantage of this process is that it makes it possible to create precise, highly complex geometries that would otherwise be either impossible or excessively expensive to achieve with traditional manufacturing.
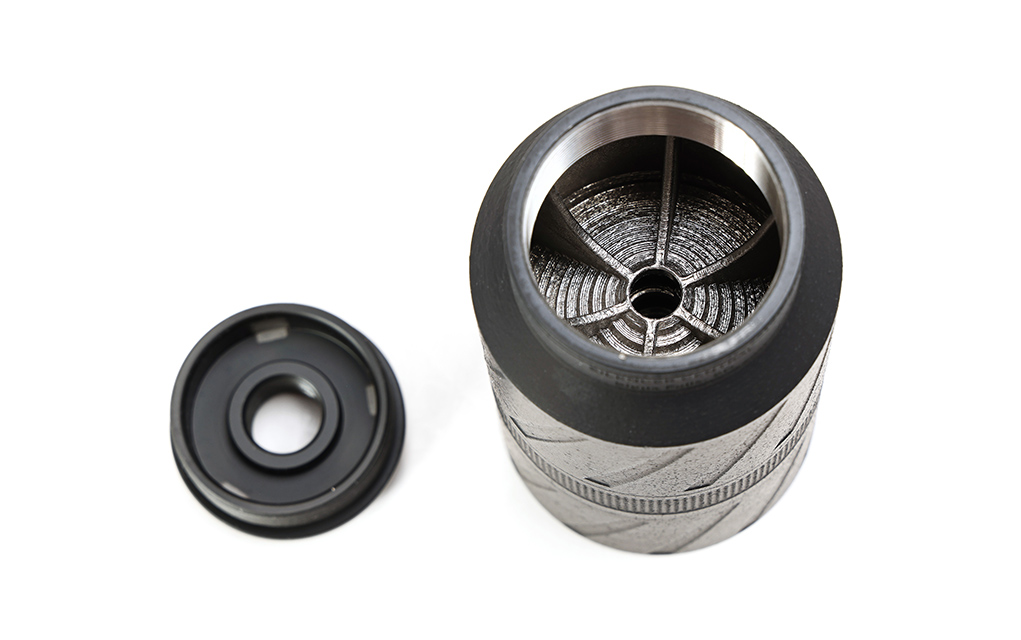
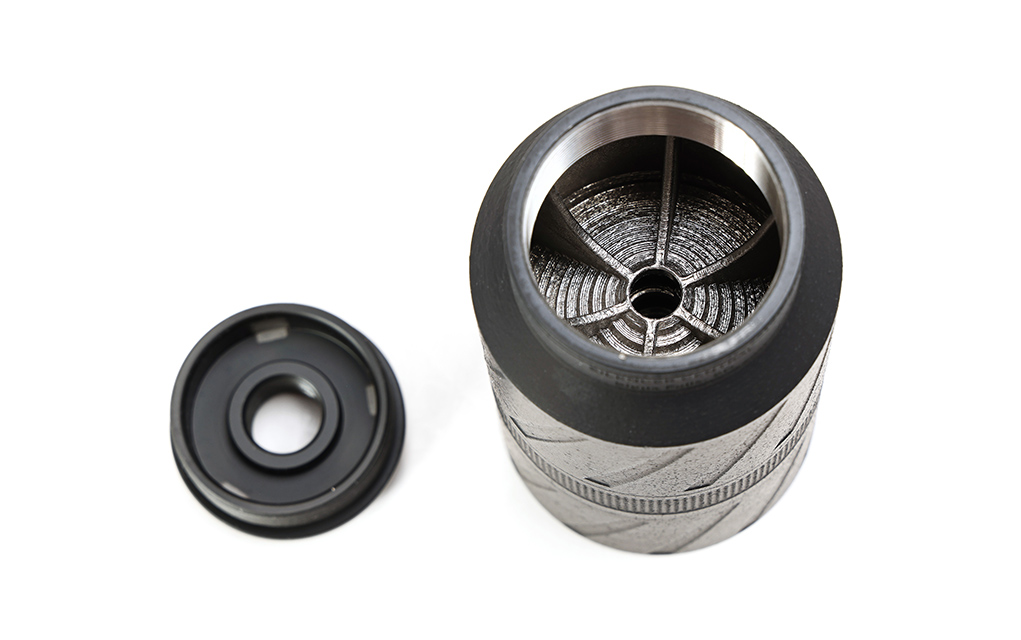
In preparing this article, we interviewed executives at Dead Air, Huxwrx, Primary Weapon Systems, Radical Defense, Silencer Central and SureFire to gather the latest insights and perspectives from those in the thick of it.
Characteristics of Suppressors
To understand why the capabilities of additive manufacturing make such a big difference in enhancing the performance of suppressors, let’s discuss some key characteristics and design goals of suppressors.
First, they’re intended to reduce the sound signature of a gun as much as possible, to mitigate permanent hearing damage to the shooter and others nearby. Not only is this a health and safety concern, but it also makes shooting much more pleasant, especially for new or sensitive shooters. Once you try hunting with a silencer, you’ll never want to go back. For society, there’s less noise pollution in the community. And for those in harm’s way, it makes it easier to communicate and harder for opposing forces to locate the operator.
Second, flash reduction is also desirable, helping to protect your vision especially in low light and under night vision. Warfighters can also minimize their visible footprint during engagements.
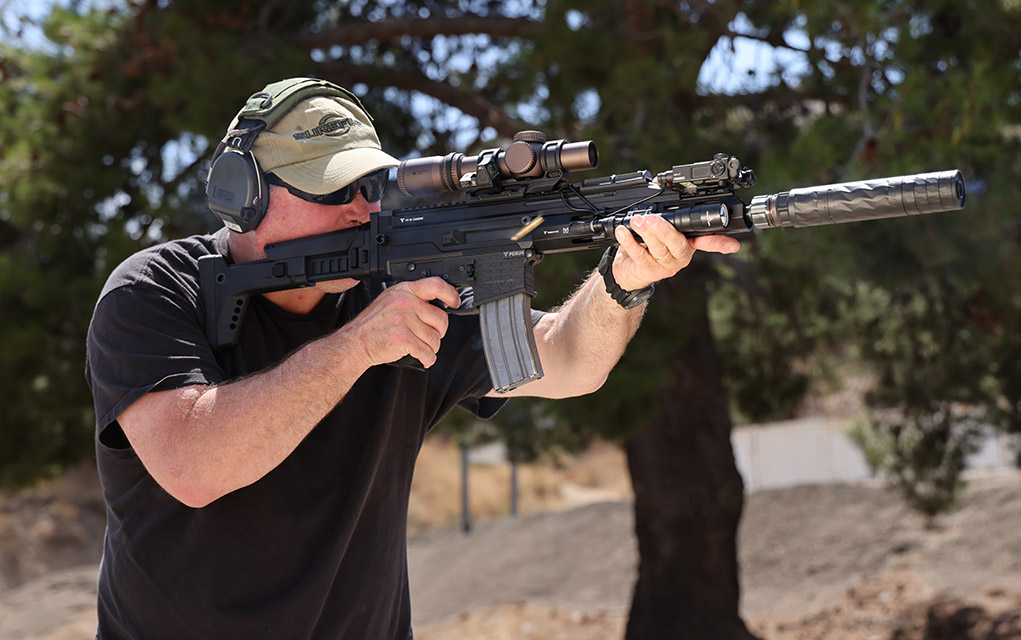
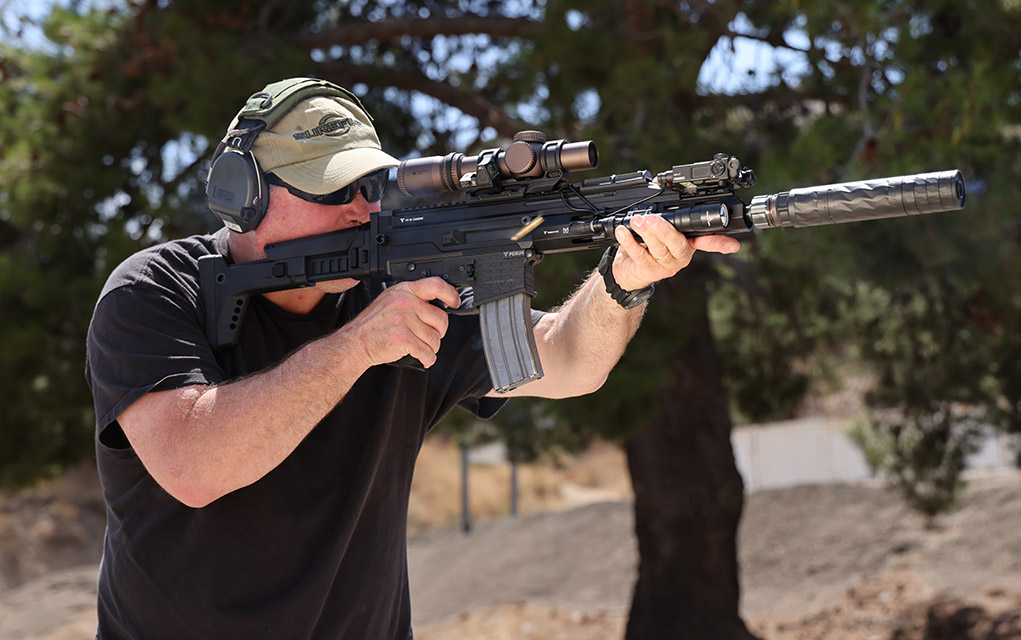
Ideally, suppressors would have minimal impact on the functioning of the host weapon, so that it operates the same (or better) with the suppressor attached than without it. For instance, it’s better to avoid affecting bolt speeds and requiring adjustable gas systems; nor do you want to pull away too much gas and induce malfunctions. For full-auto platforms, it’s best not to change cyclic rates and accelerate wear on parts. When it comes to impacts downrange, the less zero shift the better and every time the silencer is removed and reattached it should return to the same zero.
Back pressure deserves its own mention, though it technically falls under the previous category. This is a very hot topic these days, as folks have realized the negative effects of back pressure from suppressors over the years. Not only is the toxicity of increased gases coming back to the shooter a major health concern, back pressure also increases wear and fouling, thus decreasing reliability. Lowering back pressure in modern silencer designs is a key priority for many companies and a common ask from end users, agencies and militaries.
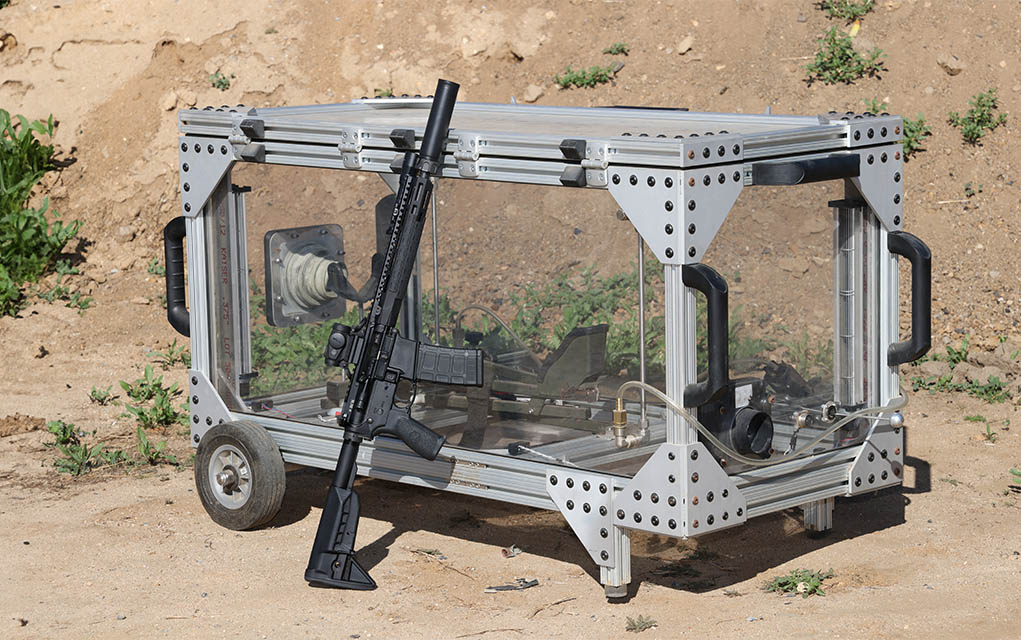
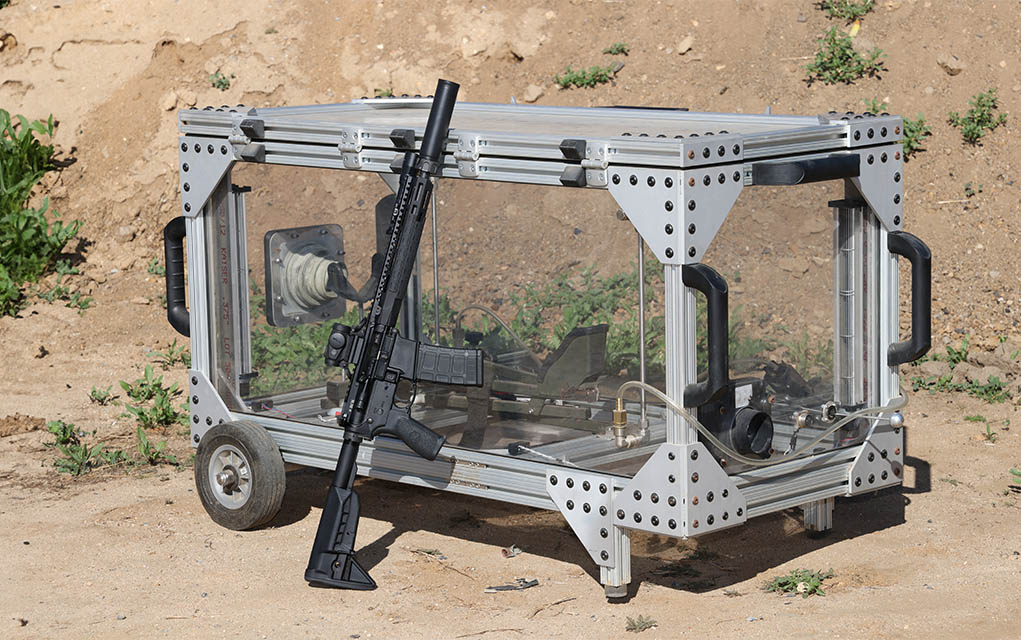
Then, there’s fundamental characteristics like durability, concentricity, physical dimensions and weight.
Juggling multiple parameters almost always involves trade-offs and compromises, as nothing comes for free. Making a change to optimize one factor will typically affect others. And everything needs to balanced against the cost to manufacture the product, as it needs to be priced appropriately for its target market with enough margin for the manufacturer.
A perfect example of those trade-offs is Silencer Central’s Speed K suppressor, which is offered in two variants: a very lightweight, non-full-auto-rated model printed from titanium and a hard use, heavier, full-auto-rated model made of Inconel. The end user can decide for themselves which mix of characteristics best fits their needs.
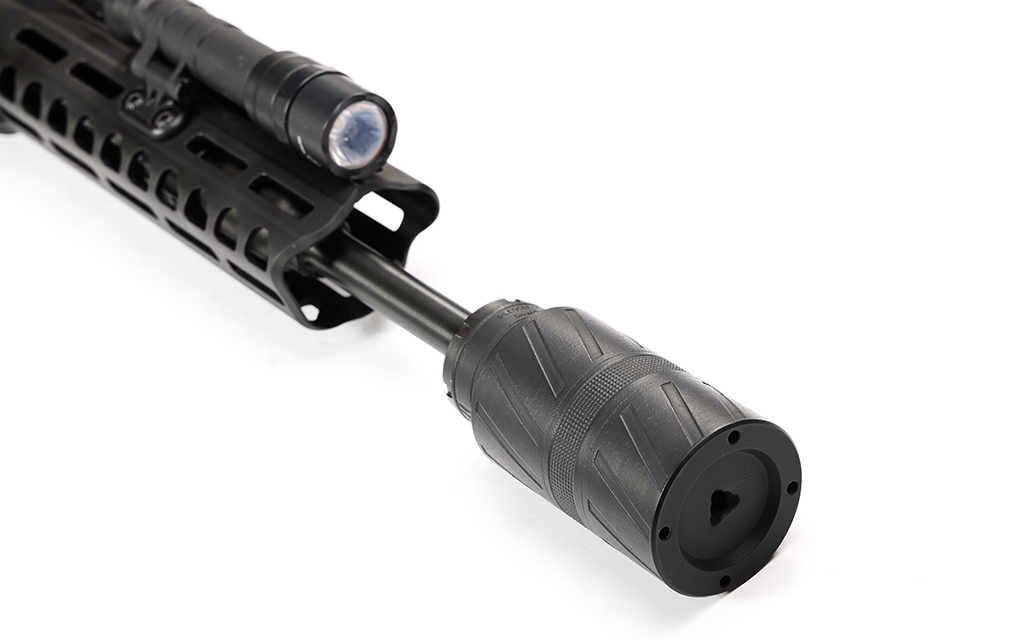
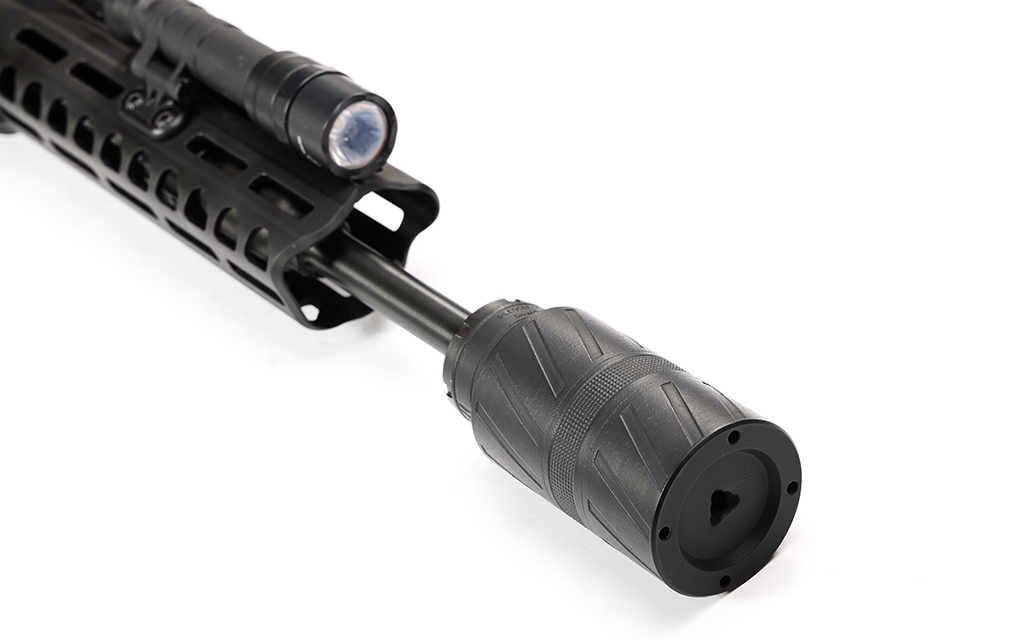
Benefits of Additive Manufacturing
Additive manufacturing is so valuable because it enables the complicated geometries that can achieve good performance across the key metrics described above, especially low back pressure. Randy Stumph, COO of Huxwrx, explained that the company had been attempting to implement various ideas for low back pressure designs for years but were unable to achieve the desired performance until they tapped into the capabilities of 3D printing. “We had a geometry problem to solve. You can print things that can’t be or aren’t practical to machine.”
It also enables rapid prototyping, as you can quickly and easily go from model to print.
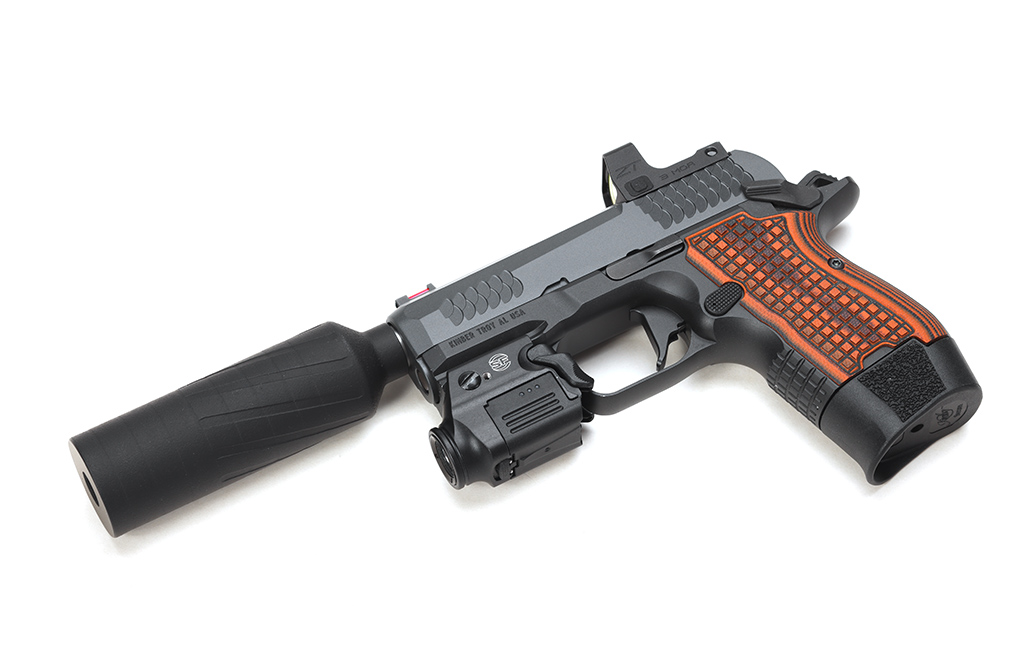
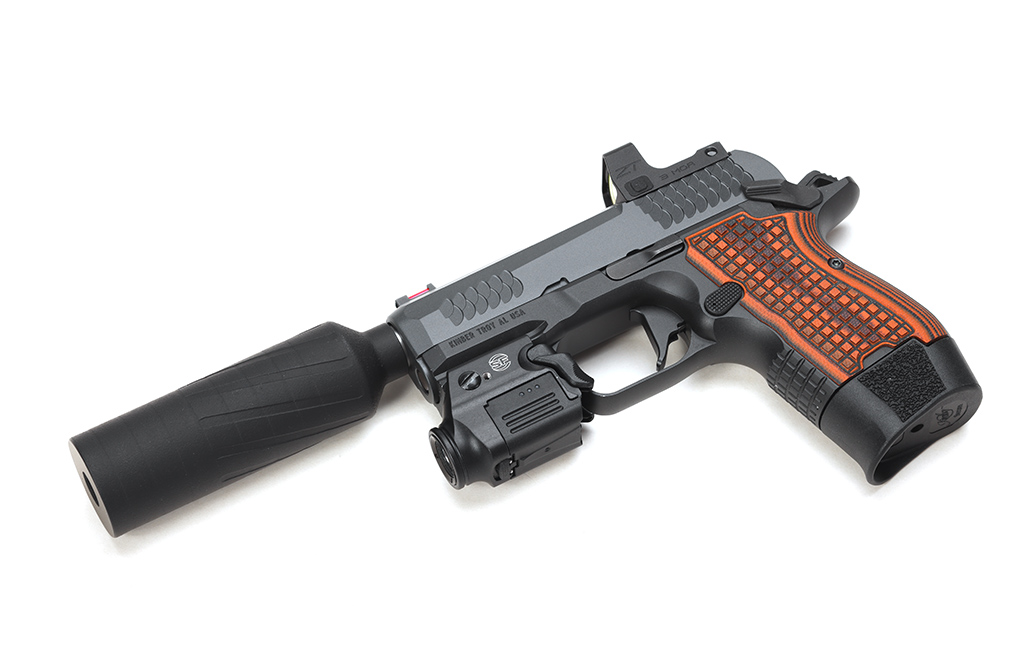
By definition, it’s more efficient in raw materials consumption, as you only use what you need with not that much waste. This is in contrast with subtractive manufacturing where you can mill away a ton of material, perhaps 80 percent of a billet. That swarf goes straight in the trash, whereas excess metal powder from printing can be processed and a good portion recycled. Printing isn’t totally efficient, as you’ll need to remove support structures and do other post-processing.
There are also materials like Inconel and Haynes 282, prized for hard-use applications, that are very difficult to machine but can be printed like any other powder.
Printing is extremely consistent and repeatable, creating extremely straight final products—this is great given the importance of concentricity with silencers. Machining is capable of even tighter tolerances, but it’s demanding to do it consistently.
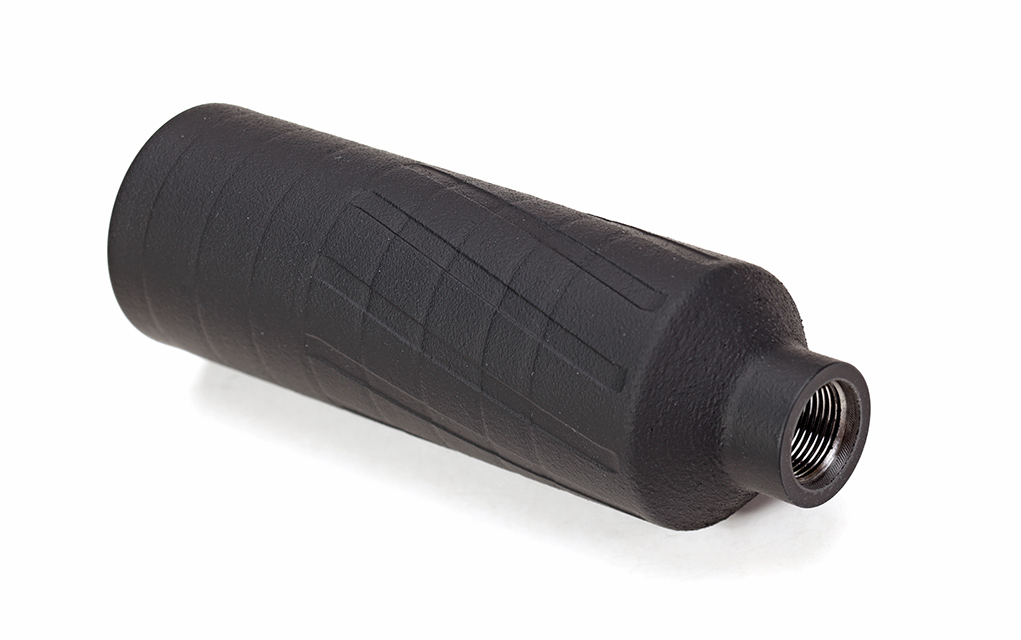
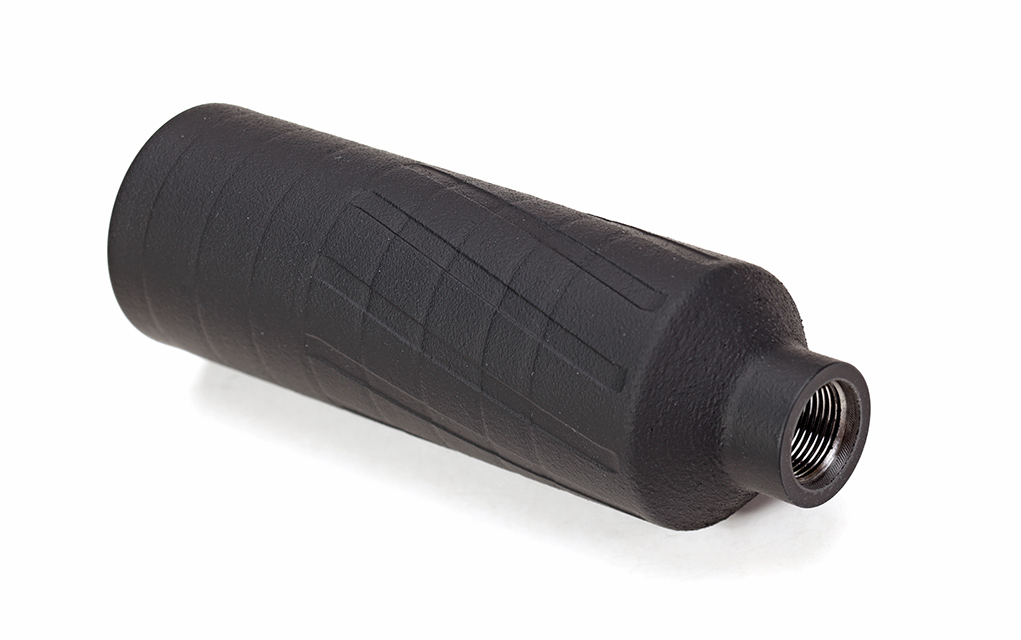
Additionally, you can continually make incremental improvements from one production run to the next if desired, since the printer just works off the file you program it with. With typical high-volume production by machining, it can be harder to make refinements to products along the way when you’ve already premade large batches of components for assembly.
Limitations and Concerns
There are some limitations and concerns related to 3D printing.
If you think about how printers put down layer after layer, from the build plate upward, this imposes some limitations on geometry such as angles and overhangs. Additionally, all of the powder needs to be evacuated from the end product, so you can’t have designs that block excess powder from getting out. All of the companies we talked to said that you just need to be cognizant of these limitations and can effectively design around them.
Surface finish is also rougher; besides the cosmetic difference, it can provide enhanced grip, heat dissipation, and shapes and textures that would be impractical to achieve traditionally.
Certain operations are still best done traditionally, such as machining threads and producing muzzle devices and adapters.
Diligent production processes and quality control are critical to ensure consistent and proper grain structure, porosity and so forth, as well as to avoid and/or detect bad layers. Many companies offer hard-use models that are 100-percent printed suppressors and heartily stand behind their durability and reliability for mission-critical use. Anyone familiar with SureFire’s product philosophy shouldn’t be surprised that they still have an outer Inconel tube wrapped around the new RC3’s mix of printed and machined innards that’s also welded to the front and back, acting as a fail-safe. Barry Dueck, their VP of suppressors and weapons, said, “As a military product, if you’re downrange on a mission, even if something happens to break, it’ll still all hold together.”
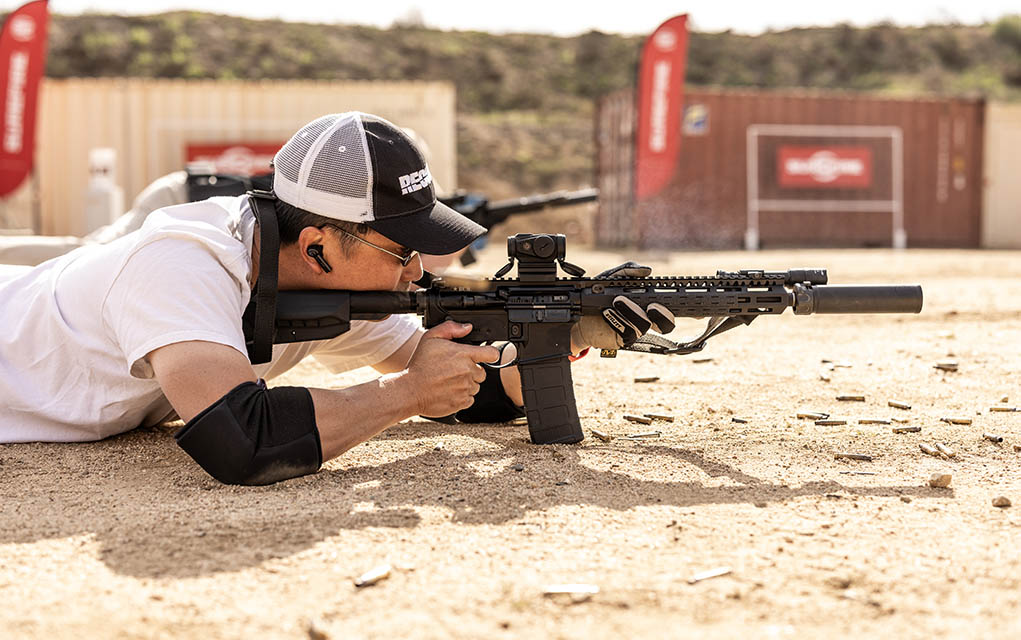
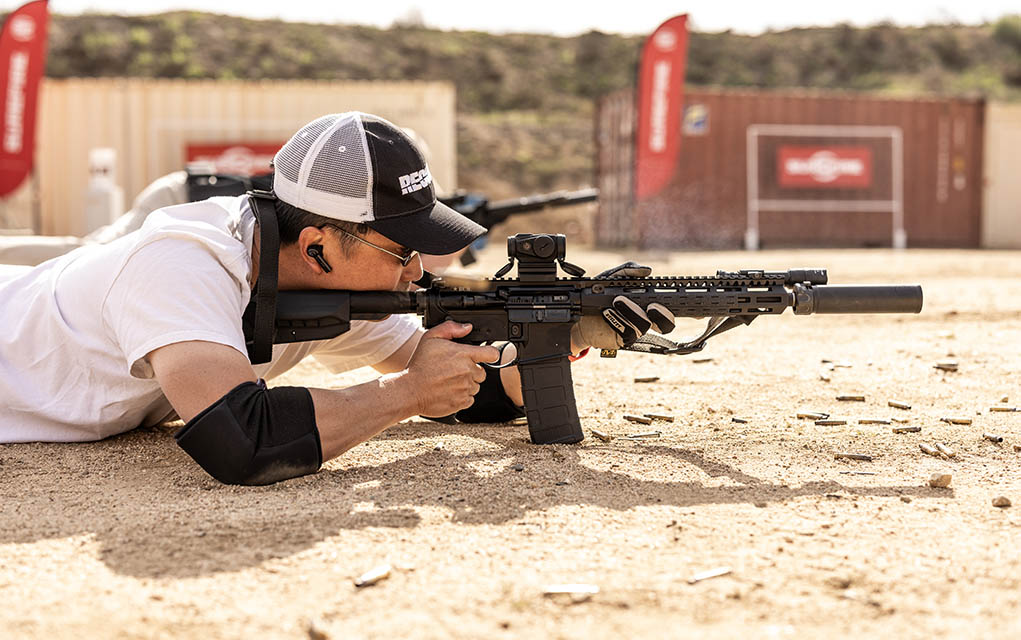
As you’d expect, the cost to manufacture printed suppressors is higher than their machined counterparts.
Vertical Integration vs. Outsourcing
Accordingly, 3D printing machines are also extremely expensive. Not only do you need to invest in the machine itself, easily $1 million and more, you need a big footprint around it in your facility; infrastructure, hazmat and support systems; argon gas; staff; learning and knowledge; and the list goes on. It’s a huge capital expenditure and commitment to do your own printing, though the payoff is capturing that extra expertise and margin. It’s no surprise that not many companies have vertically integrated in this manner. Mike Pappas at Dead Air doesn’t get too worked up over it—“Nobody’s smelting their own ore. Many manufacturers use production partners.” Dead Air’s newest Lazarus 6 is printed with ultra-durable Haynes 282.
Silencer Central sells and ships products from a wide range of brands direct to consumers, but they’ve also stood up their own product line. After initially outsourcing product development, they’ve now brought engineering in-house. Lukas VanLaecken, director of engineering, described how extremely carefully they screened and selected manufacturing partners. “It’s not just the equipment but the workforce that are important, and we’ve found partners to work closely with who are experts.” Everyone we talked to stressed the importance of being very thorough and diligent in assessing potential production partners. Dueck recounted sending the exact same sample file to several print houses and receiving prints back with different dimensions.
The software systems driving these machines are critical, and print houses learn their intricacies and how to coax the desired results, so working together closely during the design process is important.
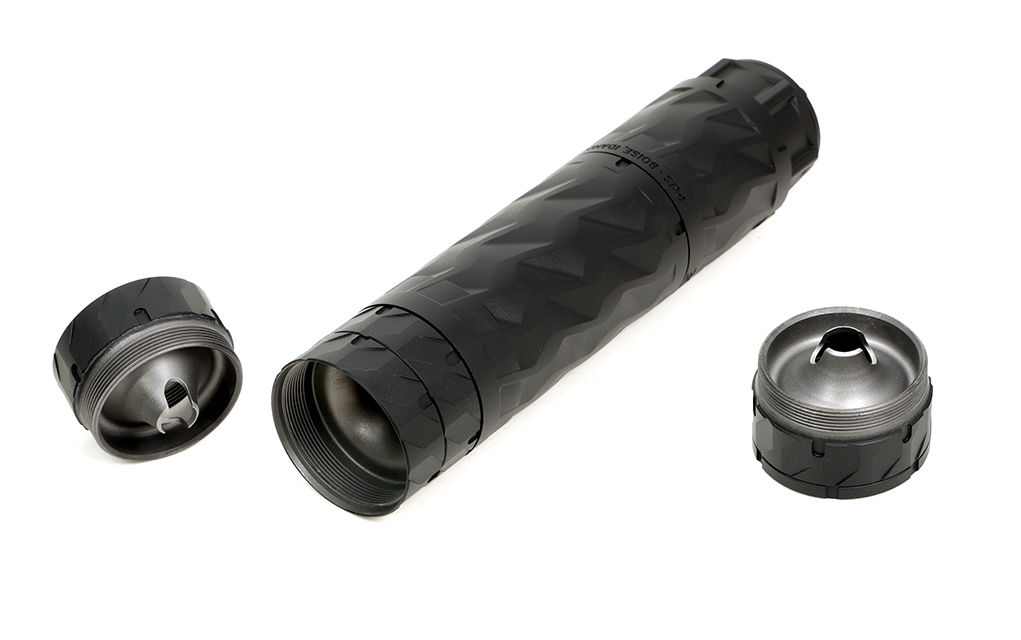
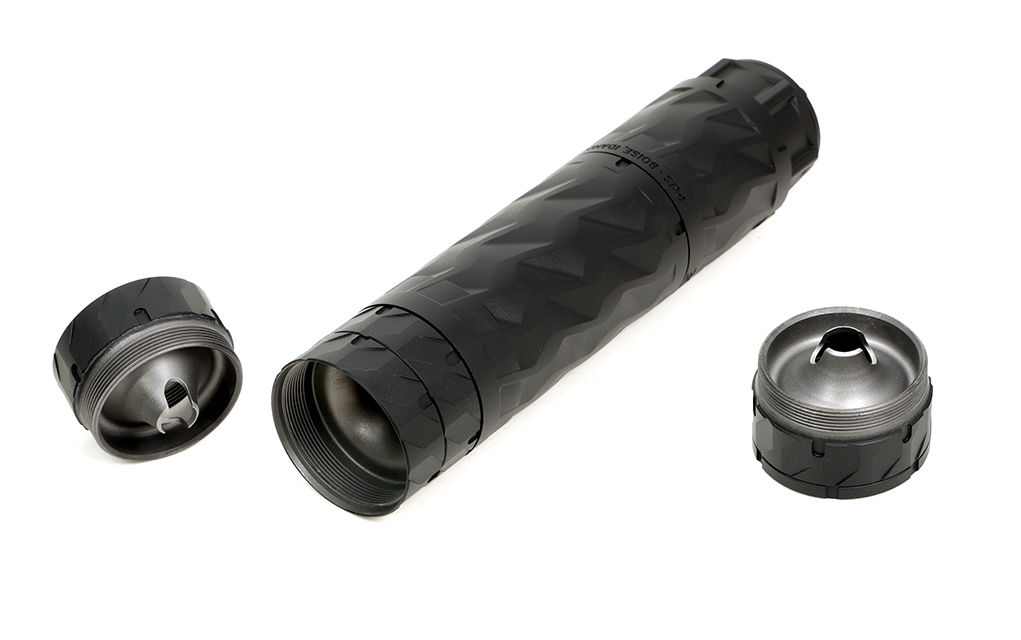
Primary Weapon Systems, on the other hand, felt a strategic imperative to own their machine and build that manufacturing capability in-house. COO Jason Curns explained, “It was a huge learning curve and so much to set up. It could go wrong in a lot of ways. That was about three years ago, and it’s already paid off. Buy once, cry once. We’re looking at buying another machine, a quad laser.” Their machine runs 24/7, cranking out nothing but PWS suppressors.
Huxwrx is synonymous at this point with their flow-through, printed silencers, but they don’t own any printers. With the volume they do, they’ve settled in the middle ground, essentially leasing dedicated manufacturing capability. They’ve contracted with key preferred manufacturing partners to have machines dedicated solely to Huxwrx production, sort of a hybrid form of vertical integration.
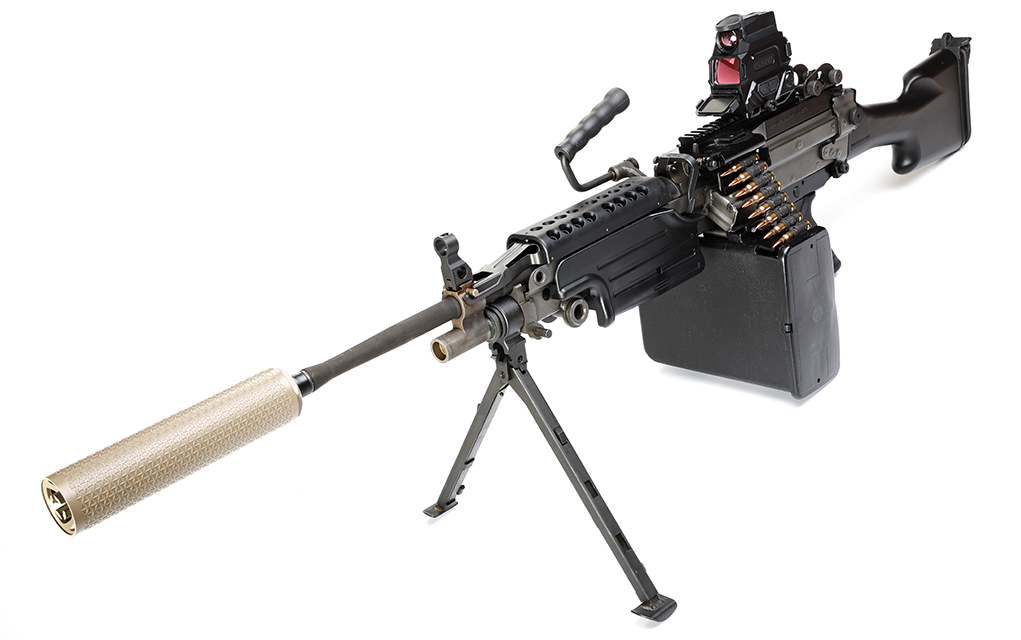
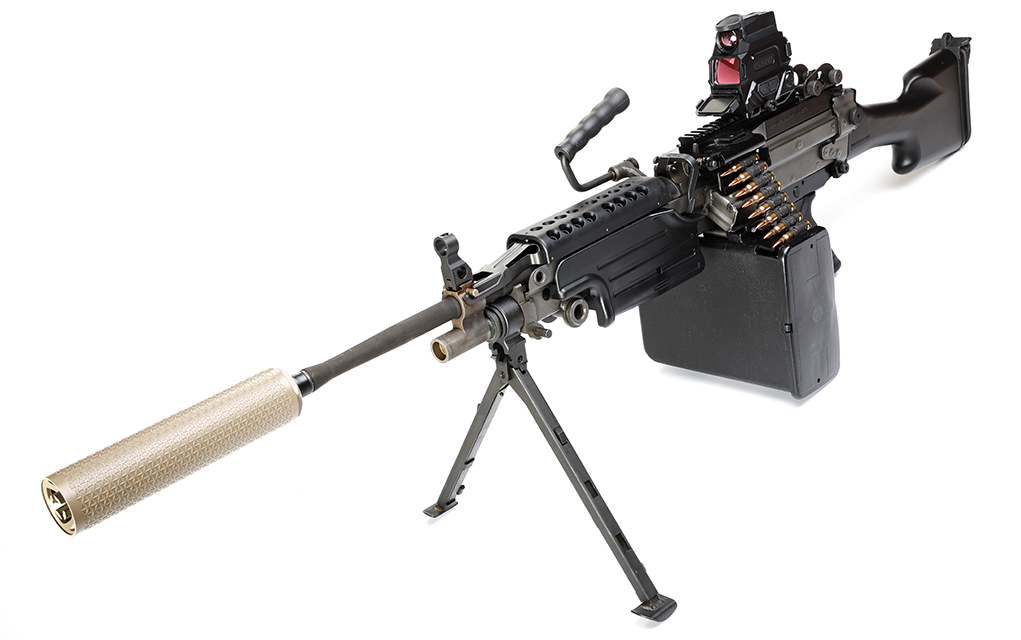
Radical Defense is an interesting case study. They initially bought a printer to work on prototyping machine gun suppressors, after tiring of paying high fees to other companies for help. After some time working with it, learning a lot of lessons, and starting to help others in the industry with their prototyping projects, Radical decided to pursue the OEM opportunity, helping other manufacturers design and print their suppressors. Five years ago, Radical Defense broke off from the original firearms business, and now over 80 percent of their revenues come from OEM customers. Less than 20 percent comes from Radical’s own suppressor line, which is primarily driven by military and law enforcement requirements both domestically and abroad.
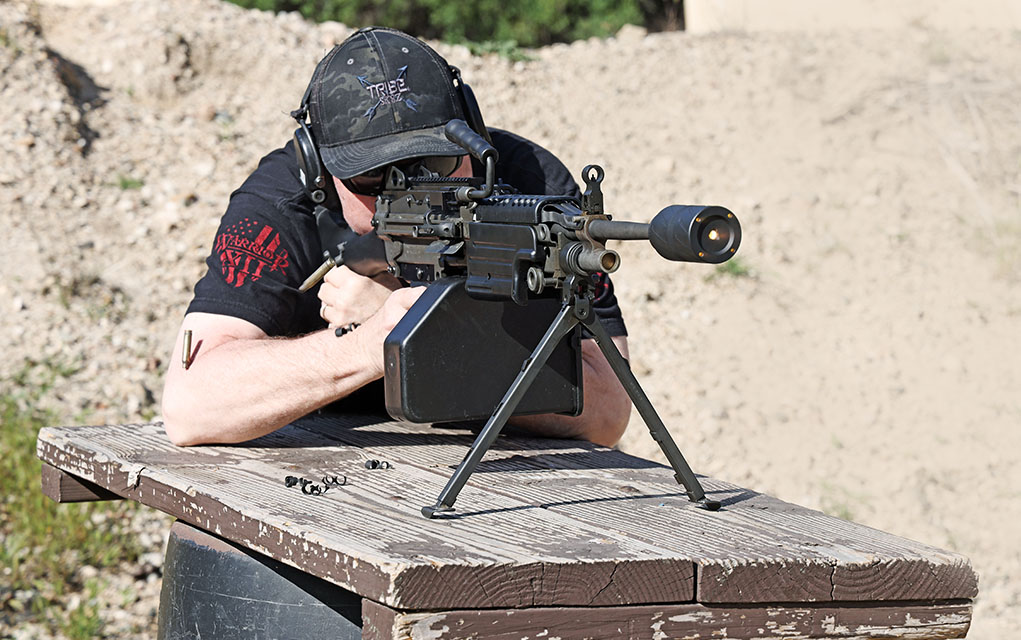
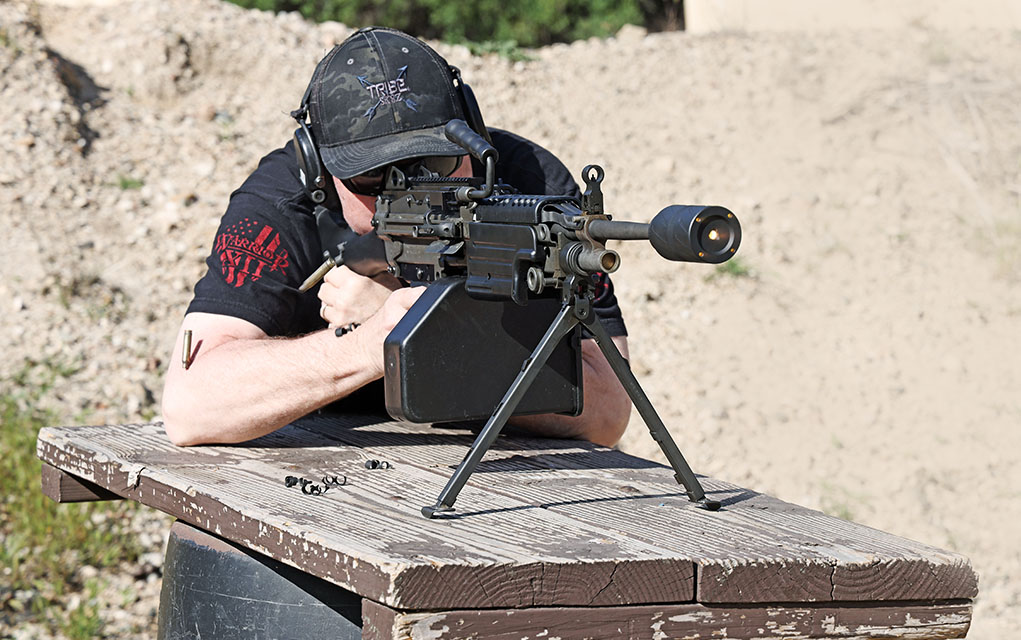
Ross Aguirre, VP of business development, and Nick Kostin, director of testing and evaluation, talked about the tremendous growth they’ve experienced. “We have seven quad-laser machines and will be growing to nine or 10 by the end of the year. They’re all running 24/7. Our OEMs keep us so busy, we often run out of inventory of our own products.”
With so much production capacity, they can also do prototyping exercises where they print a bunch of variations of a design to test and optimize it.
Looking to the Future
Just like the broader technology market, 3D printing is evolving and changing very quickly. Software is improving even quicker, adding additional capability and nuance, such as detecting spots where an abnormality like a bulge will be created and automatically compensating for it. Even with the same machines, many significant improvements have and will come purely from software upgrades.
Higher throughput will be greatly welcomed because there’s a whole lot of waiting involved in 3D printing, and shorter print times will boost production and reduce unit costs. Radical expects continuing progress on optimizing run times, laser paths and so on. Pricing for printers will likely decrease over time too, also pushing costs down.
This isn’t the death knell of traditionally machined suppressors, though. Especially if silencers are deregulated at some point, demand for low-cost options will likely increase, and machined suppressors will probably fill that segment. It would likely be a huge boom for the whole industry too, and companies won’t be able to print cans fast enough.
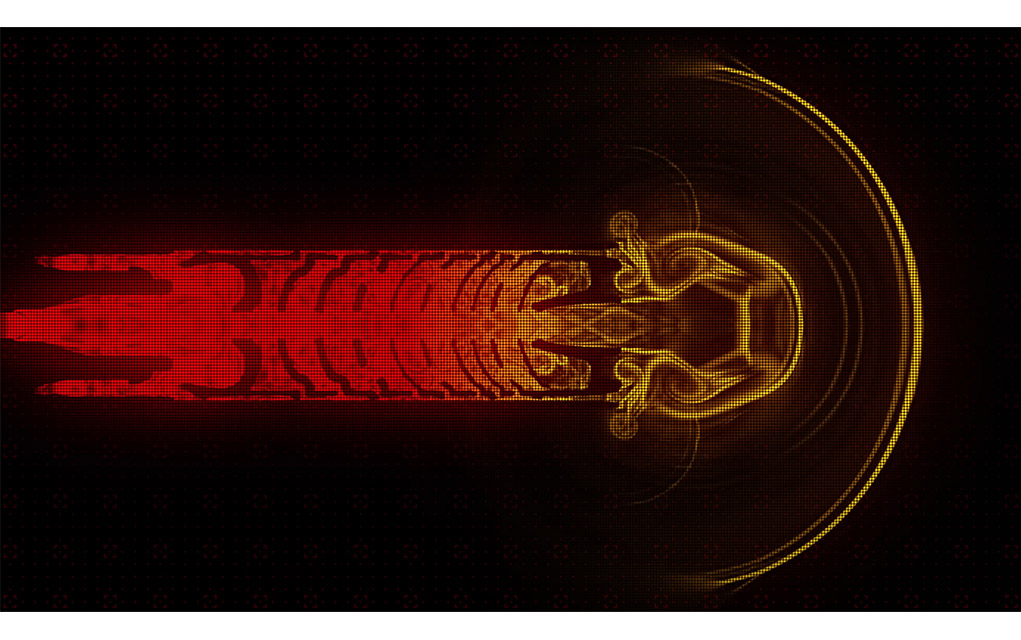
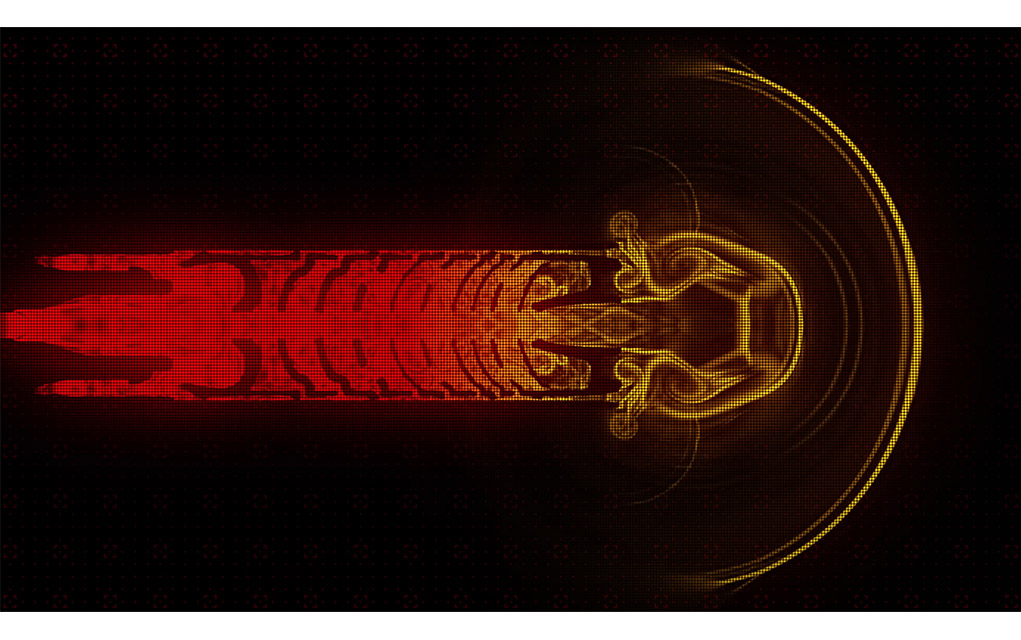
Engineers are constantly learning more about flow and geometry, and what capabilities can be pushed further for better performance. Computational fluid dynamics modeling systems keep getting better. There could be more optimization of materials for specific applications too.
There’s so much to be excited about in the coming years, as additive manufacturing continues to unlock better performance across all of the key parameters for suppressors.
Editor’s Note: This article originally appeared in the 2025 suppressor special issue of Gun Digest the Magazine.
More On Suppressors:
Read the full article here